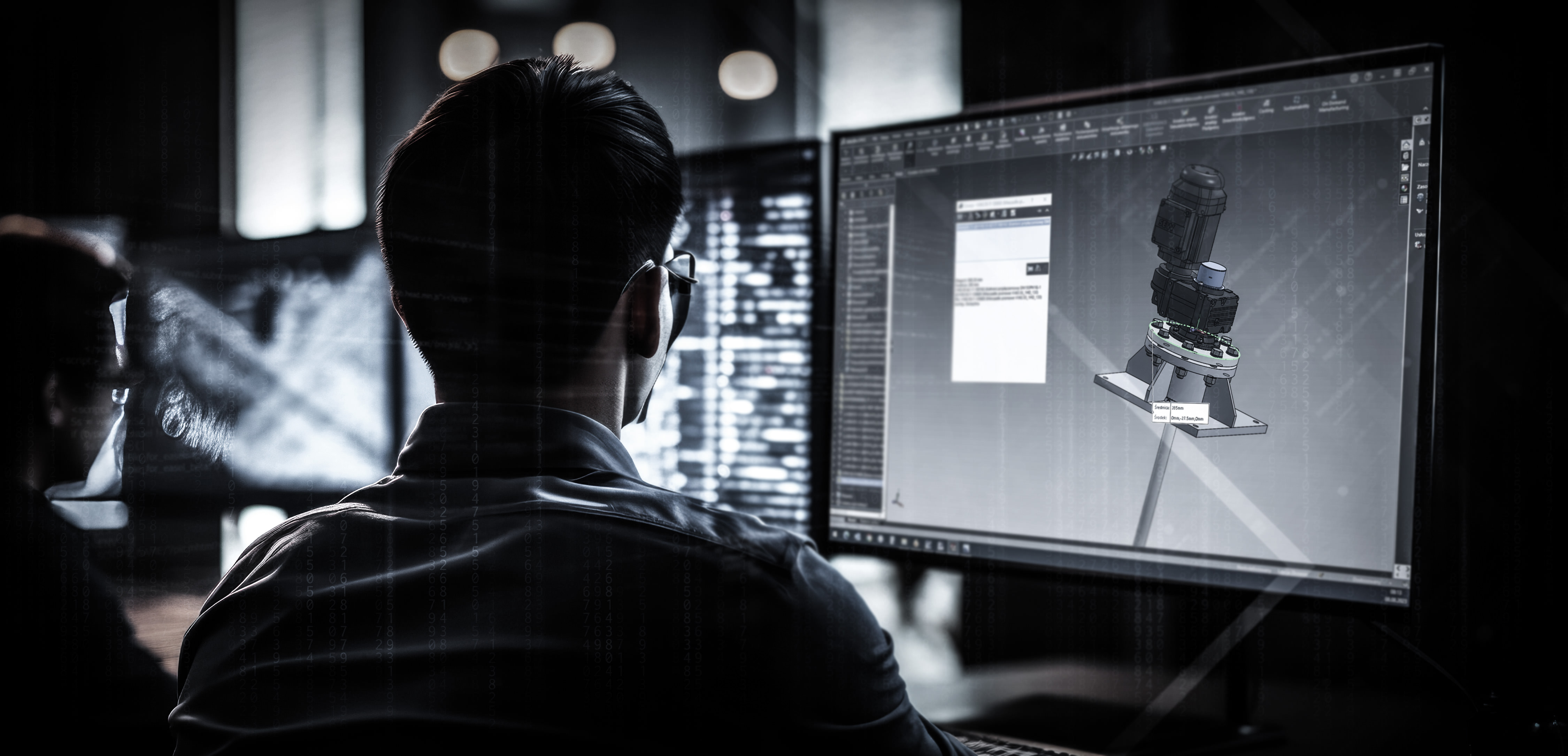
Professional top entry agitators
These solutions are widely used in the industry, being the preferred choice because of easy servicing and reliability. In order to ensure optimal mixing parameters and meet all installation conditions, these agitators can be freely configurated. REDOR's offer also includes special structures designed in response to individual inquiries, meeting the specific Client`s requirements.
Thanks to the optional quick-change mechanical seal system, the operator can easily perform service work on the mechanical seal without dismantling the drive and agitator’s shaft. Using this solution, it is possible to replace the mechanical seal without the need to use lifting equipment. Another important option, taking into account health and safety is the use of a tank sealing system during service work on the mechanical seal, in order to ensure safe working conditions for service engineers.
Technical parameters of our products
Shaft seal: | single mechanical seal, double mechanical seal with barrier liquid installation, lip ring, gland packing, water labyrinth seal |
Agitator drive: | direct from the electric motor, gearbox transmission, belt transmission |
Material inside the tank: | carbon steel, stainless steel, Nickel alloys (e.g. C-276 / C-22), stainless steel dedicated to the power industry (e.g. 926), titanium, rubber linings, PTFE coatings, other specialized coatings. |
Maximum total shaft length: | 18000mm (individual analysis for longer lengths) |
Maximum impeller diameter: | 5200mm (individual analysis for larger diameters) |
Our selected services and devices
2022
- delivery and installation of top entry agitators for the adhesive dispersion installation
- delivery and installation of top entry agitators for the resin reactor
- delivery and installation of top entry agitators for the resole resin reactor
- delivery and installation of top entry agitators for organic acids
- delivery and installation of top entry agitators for triethyloamine
- delivery and assembly of top entry agitators for polyol synthesis
- delivery and assembly of top entry agitators for polymer synthesis
2021
- delivery and assembly of agitators for synthesis reactors
- delivery and assembly of a agitators for the polyol neutralization reactor
- delivery and installation of agitators for lime milk tanks
- delivery and assembly of a agitators for the polyester neutralization reactor
- delivery and installation of agitators for resin line sewage tanks
2020
- delivery and installation of agitators for the windshield washer fluid installation
- delivery and installation of a top entry agitator for tanks of contaminated ethanol
- delivery and installation of a top entry agitator for tanks for zinc blend suspension
- delivery and installation of a top entry agitator for distillery mash installations
- delivery and assembly of the agitator for the acidification agent tank
2019
- delivery and assembly of agitators for polyol installations
- delivery and installation of top entry agitators for the flue gas desulfurization installation
- delivery and installation of agitators for storage tanks
- delivery and installation of top entry agitators for gypsum suspension installations
- delivery and installation of a top entry agitator for the tank with ice water
- delivery and assembly of top entry agitators for water dispersion of polymers
2018
- agitators for a continuous FDO installation for periodical Oxoviflex production
- delivery and installation of agitators for latex installation
- delivery and assembly of agitators for the coal sludge installation
- delivery and installation of agitators for the flocculator installation
- delivery and assembly of a top entry agitators with a slag installation tank
2017
- delivery and installation of 40 agitators for the Water Treatment Station
- delivery and installation of top entry agitators for FGD
- delivery and assembly of agitators for zinc blende
- delivery and installation of agitators for FGD at the Waste Utilization Plant
- delivery and installation of top entry agitators for polyester installations
- delivery and installation of 4 agitators with tanks for the ash suspension installation
17.538,5mm in length inside the tank
The longest segmented shaft manufactured in our factory measures
ATEXQ Quality Certificate
In close cooperation with accredited certification bodies, we design and manufacture mixing units operating in explosion hazard zone "0".
CARE FOR DETAILS AND MATERIALS
determines the direction of production
Qualified machine operators, modern machinery fleet, machining engineers supported by CAM technology and 100% control measurements of tolerated actual dimensions ensure compliance of manufactured details with technical documentation. Combined with high requirements for suppliers of steel and commercial technical components, we ensure stable and high quality of the offered products
